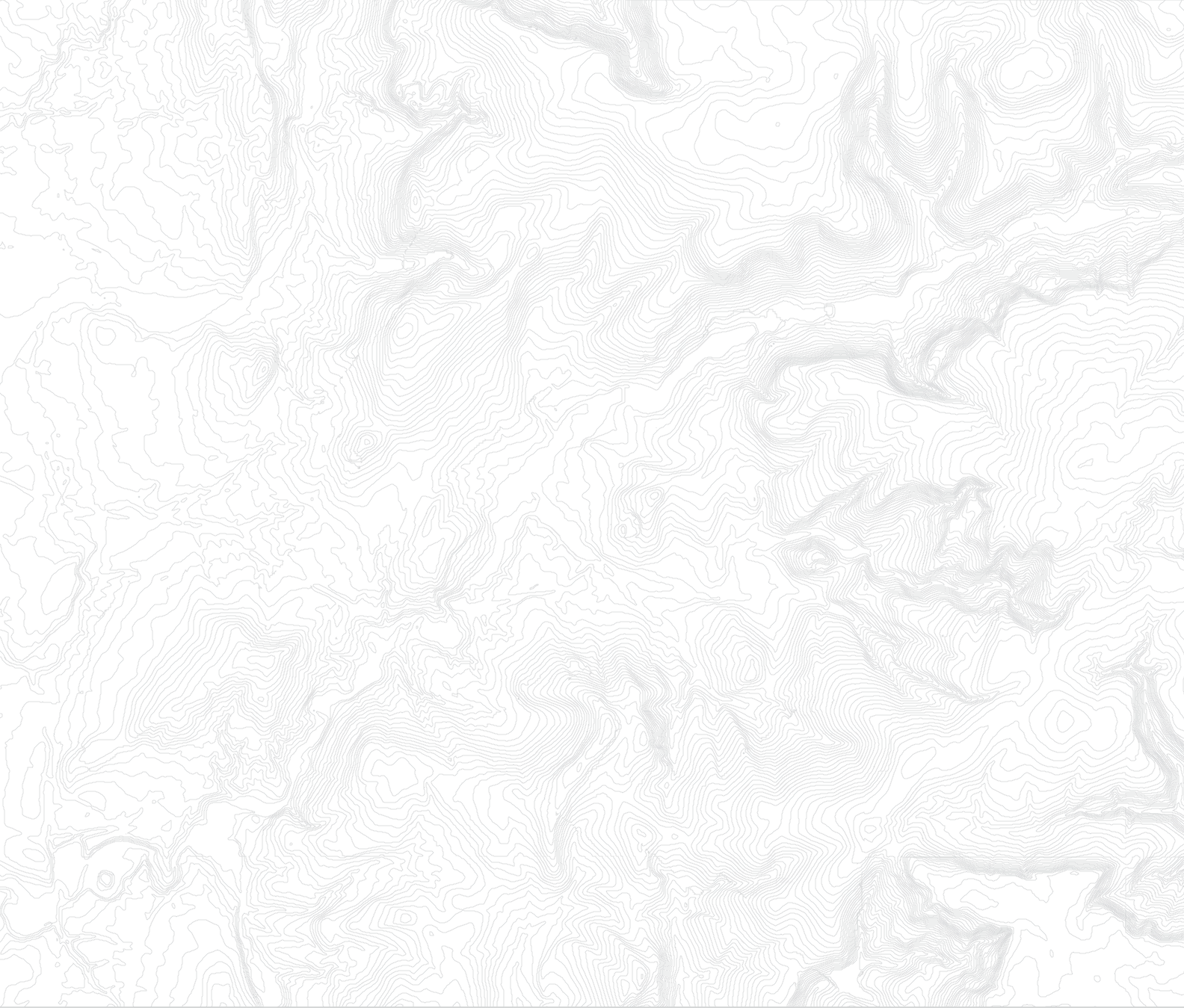
Understand Your Blades & Assets
Measure | Analyse | Optimise
What We Do
-
We offer a range of sensors for data capture including accelerometers, strain gauges and GPS.
High specification digital accelerometers
Tempory or permanent installation
Wired RS485 and wireless radio
Versatile and expandable
SD and local storage
No calibration
Low cost
-
Damage detection and changes to structural characteristics
Comparative changes by type or over time (supported by machine learning)
Event detection (e.g. bird strikes, abnormal movement)
Frequency response and transmissibility (defect detection such as bond failure)
-
Find issues before they cause problems. Such as:
Abnormal Vibrations
Fatigue Accumulation
Change in Characteristic Movement
Altered Transmissability
-
Our approach of spotting problems in your assets early enables more cost effective scheduling of repairs.
When monitoring a group of assets, maintainance decisions can be made depending on how many assets need attention, and if the issue can be temporeraly mitigated in a different way.
Our continuous monitoring system enables defects to be found early, and inspection can be targeted rather than scheduled.
For a low upfront cost, our IoT device can significantly lower the maintainance costs of your assets during its lifetime.
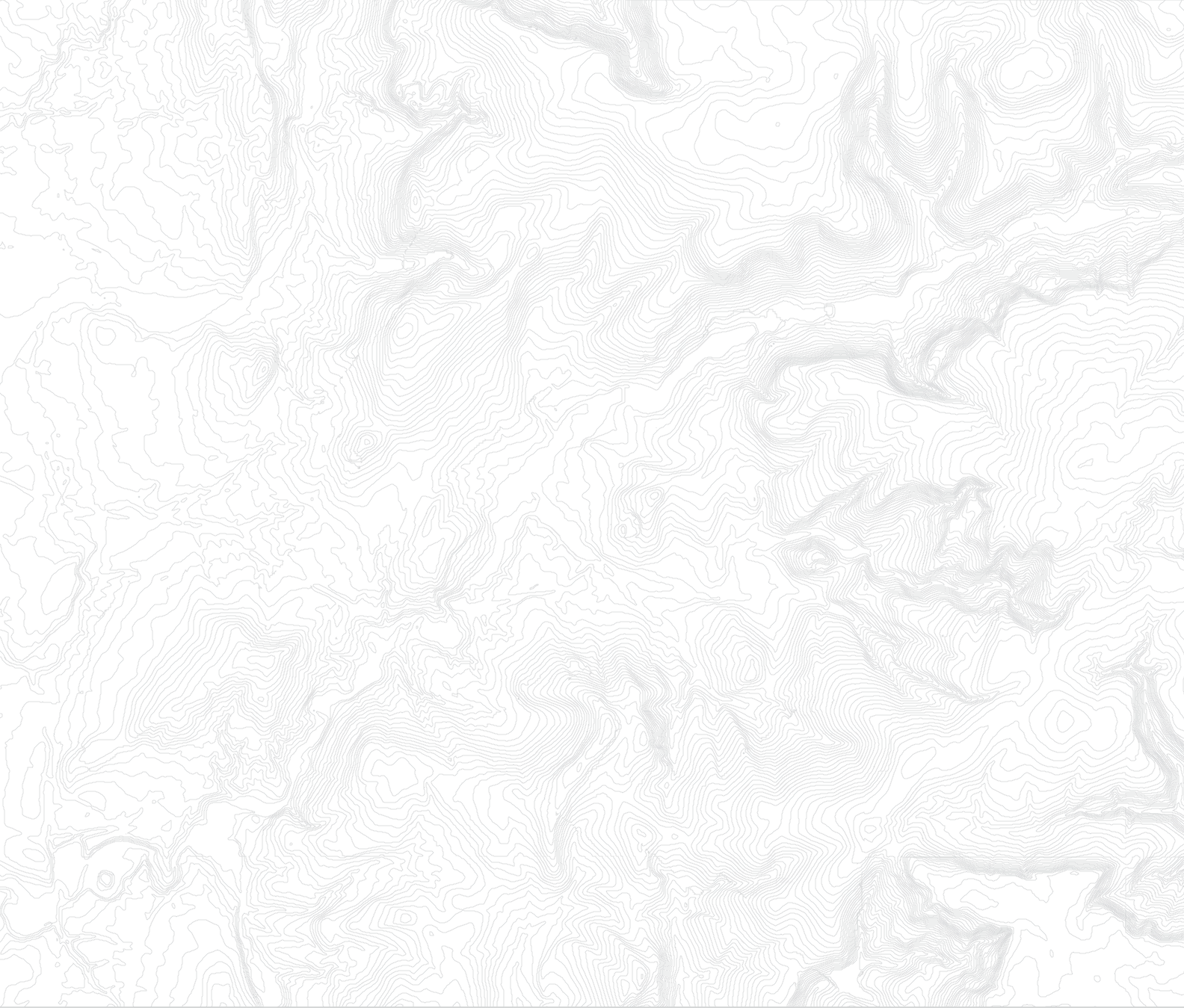
Sense
Lab quality sensors
Low cost
Reliable
Easy and fast to install
+
Analytics
Physics based & machine learning tools
Identifying:
Changes in blade dynamics/structure
Damage inducing conditions
fatigue accumulation
Modelling:
Blade movement
(Azimuth, flex, twist and resonance)
Comparing:
Behaviour over time
Against other blades/turbine/fleet
+
Report
Actionable insights
Providing visibility in the field only usually available on test blades
Informing and guiding interventions at site
Informing blade/turbine life extension

What we have detected
-
Rotor Behaviour
Blade behaviour can be shown throughout the lifespan of the blades allowing changes over time or between blades to be observed, quantified and diagnosed.
●Interaction can be observed between blades
●Blade twist can also be animated
-
BladeCracking
Observed a persistent anomaly in the frequency response of one blade compared to the other two.
Encapsulated the magnitude of this anomaly in a metric.
●Successfully detected a sub 1m crack 3 weeks before detection by drone.
●The initial detection was preceded by an unusually high-energy event.
-
Cumulative Vibration Exposure (CVE)
ELEVEN-I Kinetic Energy Tool can be used to quantify the “work done” by blades to provide a metric for fatigue accumulation.
●Identify periods of interest
●Compare blade to blade
●Compare turbine to turbine